La recherche de la qualité a toujours été un but principal pour les entreprises du BTP
Tout projet de construction réunit trois intervenants principaux : le maître d’ouvrage, le maître d’œuvre et les entreprises. Au sujet de la qualité des ouvrages bâtis en France, la plupart d’entre eux l’estime satisfaisante et pense qu’elle va encore s’améliorer.
« La non-qualité dans le bâtiment coûte quelque 10 milliards d’euros par an. »
Source : Agence qualité construction
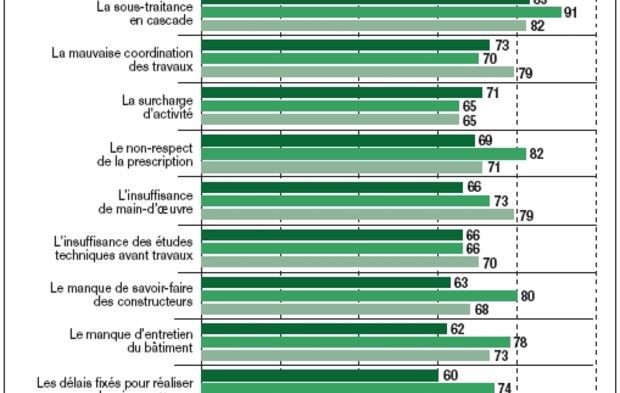
Les litiges surviennent lors de :
➡️ Malfaçons (43%),
➡️ Gestion de cas de non-conformité (22%),
➡️ Retards (20%).
En détail, la liste des points concrets défectueux à reprendre est longue. Les désordres trouvent aujourd’hui rarement leur origine dans des produits défectueux mais plutôt dans des défauts lors de la mise en œuvre. Et c’est souvent l’organisation de l’ensemble de la filière qui est mise en cause:
« Les multiples attentes de plans d’exécution non produits en temps et en heure » et le cas d’une opération décrochée pour seule raison de démarrage immédiat, mais réellement non démarré des mois plus tard ! «
Finalement, la non-qualité dans le #bâtiment coûte quelque dix milliards d’euros par an, soit environ 10% du chiffre d’affaires du secteur.
Finalement, la non-qualité c’est quoi ?
La non qualité réside dans l’inaptitude à répondre aux attentes des entreprises, des clients ou des usagers.
Elle peut être subie suite à des défaillances de processus, une inadéquation de compétences ou de ressources, face à la contrainte de la concurrence ou la pression d’un client.
Le problème c’est que cette non-qualité a un coût … Ou plutôt la non-qualité a DES coûts.
Quand on parle du coût que cela peut engendrer, on pense naturellement à l’esprit au coût financier direct, celui qui se traduit par un flux monétaire réel.
… Mais les coûts financiers cachés ne doivent pas être négligés
Les pénalités, les surcoûts liés au retour à la normale, les couts de la gestion des réclamations, le « gaspillage » du temps et surtout le manque à gagner.
Sans parler d’impact sur l’image et la mauvaise réputation qui complexifient et renchérissent la recherche de nouveaux clients.
Un autre coût souvent négligé:
Le coût social: La non-qualité entraîne une surcharge de travail au sein des équipes. Ce travail fastidieux consistant souvent à corriger des erreurs dont le collaborateur ne se sent pas responsable. Du coup, il vit cette tâche comme une corvée voire une punition.
Comment en sommes-nous arrivés à ce degré de non-qualité dans le BTP ?
1- Un manque certain de communication :
Les réunions autour d’une table où nous faisons la synthèses thème par thème disparaissent, les innombrables mails les ont remplacées dans un jeu de ping-pong. Au lieu d’un « dialogue ouvert » pour une « volonté commune d’aboutir vers une satisfaction du client, chacun campe sur ses positions et ses certitudes ».
2- Une formation inadaptée et les profils non disponible :
Autre sujet de préoccupation surtout pour les dirigeants de TPE-PME
Réussir la qualité dans la construction
Baisser ses coûts de non-qualité est une source importante de profitabilité pour les entreprises. Pourtant elles sont encore trop peu à savoir comment mesurer ces coûts, encore moins à engager des actions pour les réduire.
Une organisation collaborative favorisant l’échange et l’implication de chacun
Il est important de constituer une équipe compétente pour analyser les risques et les anticiper. Aussi l’organisation de réunions de planification afin de favoriser l’échange d’informations – notamment pour analyser et anticiper les risques – et l’implication de chacun.
Une organisation de projet par flux
Un problème de non-qualité implique bien souvent une pluralité d’acteurs et a pour origine des causes organisationnelles multiples. Les principes clés pour les réduire ici sont l’anticipation, la préparation, la collaboration et le pilotage de l’organisation. La coactivité est-elle visible sur le planning ou les supports de réunion ? Le choix des lieux de stockage est-il soumis à la concertation entre les intervenants ? Le délai de validation technique du procédé permet-il d’approvisionner le matériel à temps ?
Même si les entreprises sont conscientes que les coûts de la non qualité sont importants, ces sujets restent encore peu discutés car il y a un sentiment de culpabilité autour de la non-qualité, le droit à l’erreur reste un sujet compliqué en France.
Growline, réseau de BET et d’ingénieurs OPC, garantit un meilleure résultat grâce à un cheminement en trois étapes : optimisation des besoins avec des séances de remue-méninge avec tous les intervenants, choix des meilleures options en amont, et réduction des coûts et des délais grâce à une anticipation des risques et une meilleure réactivité.M